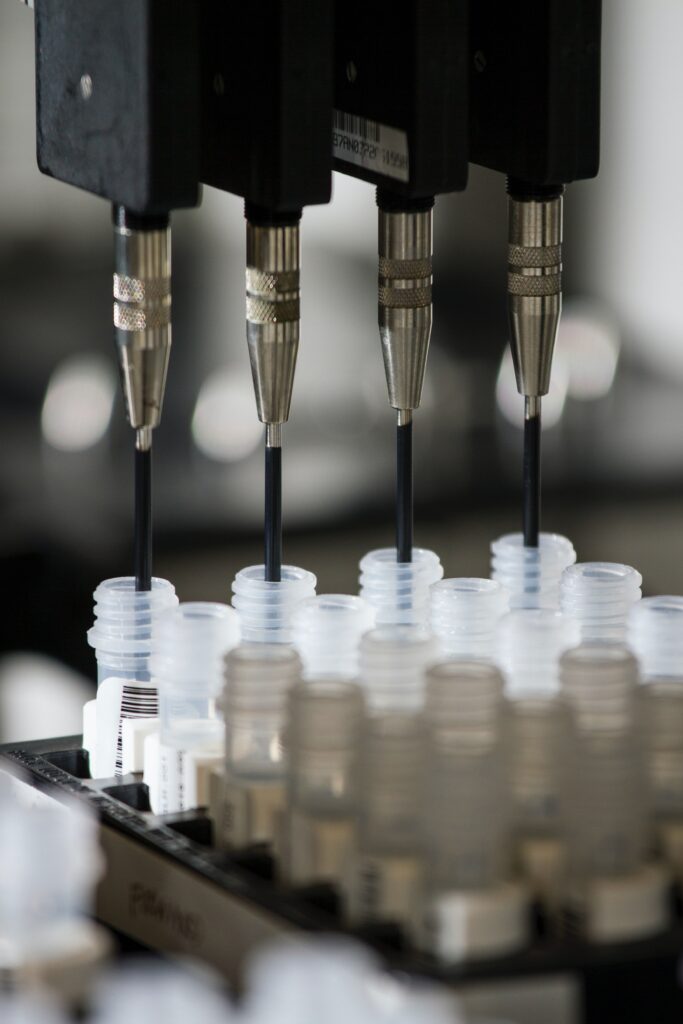
Lab automation has become more and more popular recently mainly due to the demand for high throughput screening and testing. In most cases, when people talk about lab automation, they are referring to liquid-handling systems. As the name indicates, liquid handling systems, also known as liquid handling robots or automated liquid handlers, are robotic devices used to automate the precise, repetitive, and accurate transfer of liquid volumes. These days, you can find these instruments in drug discovery, chemical synthesis, bio-assay labs, and virtually any lab that performs repetitive liquid handling tasks.
A liquid-handling robot can be as simple as a standalone benchtop automated pipett (such as Integra Assist Plus) or it can center a complex end-to-end automated workflow by integrating various instruments (such as those ones that can be found in BioFoundries). Nevertheless, the main feature of a liquid handling robot is to offer accurate liquid transfer (no surprise!). So, various mechanisms and technologies have been developed to accurately and precisely transfer liquid volumes. The choice of mechanism depends on the specific application, the required precision, and the type of liquid being handled. Here are some common liquid-handling technologies used in modern liquid-handling robots:
- Air Displacement Pipetting: This mechanism relies on air pressure differentials to aspirate and dispense liquids. A pipette tip is used to aspirate the liquid by creating a vacuum in the tip, and the liquid is dispensed by releasing the vacuum and allowing air pressure to push the liquid out. This method is widely used for general liquid handling tasks and is suitable for a broad range of liquid viscosities. This is the main liquid handling technology in the Hamilton robots.
- Positive Displacement Pipetting: Positive displacement pipetting mechanisms use a disposable, disposable piston to physically displace the liquid into the pipette tip. This mechanism is ideal for handling viscous or volatile liquids and reduces the risk of cross-contamination. You can find this mode in various Formulatrix instruments.
- Peristaltic Pumping: Peristaltic pumping involves using a rotating roller mechanism to compress and decompress tubing, creating a flow of liquid. It is often used for dispensing large volumes of liquids and for applications where avoiding contact with the liquid is important. This is more common in reagent dispensers where accuracy might not be critical.
- Piezoelectric Pipetting: Piezoelectric pipetting relies on the deformation of piezoelectric material to dispense precise nano-liter or pico-liter volumes of liquid. This mechanism is commonly used in droplet-based microfluidics and high-throughput screening applications. Check BioSyntheSizer from GeSiM.
- Acoustic Liquid Handling: Acoustic liquid handling uses ultrasonic sound waves to dispense and transfer liquids without any physical contact with the sample. It is highly precise and avoids the risk of sample carryover. Beckman Eco is an example of this mode.
- Syringe Pumping: Syringe pumps use a plunger within a syringe to draw in and dispense liquids. This mechanism is suitable for both small and large-volume liquid transfers and is often used in high-throughput applications. This is a common technology in some of Tecan’s liquid-handling robots.
These are some of the more common options, but there are additional technologies, with some still in development, in the market. Examples include capillary action and contactless magnetic or electrostatic manipulation, which are often used in microfluidic and lab-on-a-chip systems.
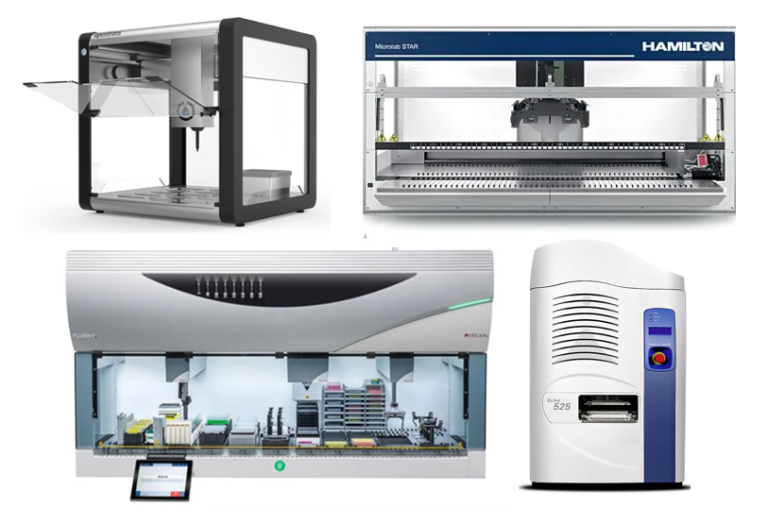
If your lab is new to liquid-handling robots, here are a few thoughts on selecting the right robot:
- Accuracy and Precision: The robot should offer high accuracy and precision for your liquid type and working range. Pick a robot that can handle various liquid types, including aqueous solutions, organic solvents, viscous liquids, and volatile reagents. Hamilton STAR and Tecan Evo systems are robust choices for most applications. Whereas, for viscous liquids robots that utilize positive displacement pipetting can be a better choice.
- Throughput: Consider the robot’s throughput capabilities. Choose a robot that can meet your sample processing needs, whether it’s low, medium, or high throughput. If your task is only to handle a few samples or execute simple commands, a benchtop simple liquid handler such as Integra Viaflo or Opentrons might suffice. Consider the robot’s deck capacity and the number of labware positions available for various types of containers (e.g., microplates, tubes, reservoirs).
- Modularity and Integrability: If you consider upgrading to fully automated workflows, or need the flexibility to support several assays on the same instrument then opt for a liquid handling system that is modular and customizable. This allows you to adapt the system to various applications and tasks. Hamilton and Tecan systems usually offer the best compatibility and options for third-party-developed devices (such as robotic arms), API, and software such as schedulers. Some systems are highly customized out-of-the-box for certain applications, such as NGS.
- Software Interface: the user interface and software should be user-friendly, allowing for easy programming, customization, and monitoring of liquid handling protocols. The more complex system provides more flexibility but they need a well-trained operator to utilize. On the other hand, drag-and-drop systems need only a few hours of training. Some of the instruments, such as Opentrons, offer programmability in popular languages such as Python. This offers flexibility to automate scripting for simple tasks using generative AI tools such as ChatGPT https://insights.opentrons.com/webinar-07-25-23-chatgpt
- Compatibility with Labware: ensure the robot is compatible with a wide range of labware, including pipette tips, microplates, and sample tubes. For some vendors, the only option is authentic consumables whereas for some there are several generic alternatives. This factor will affect operation costs in the long term. One can 3D-print custom labware and carriers, but always check if the labware and carriers that you would need for the task exist for that instrument.
- Sample and Reagent Tracking: If you need sample management, perform multi-step processes, or work with many samples (HT) consider the ability of the robot to track samples and reagents throughout the workflow. Hamilton system offers excellent file-handling capabilities although it needs skills to program it. This feature will also help with data management, reporting, and LIMS integration.
- Validation and Regulatory Compliance: If working in regulated industries (e.g., pharmaceuticals, clinical diagnostics), ensure that the robot, both software and hardware, meets the necessary validation and compliance requirements. Check for FDA Regulation 21 CFR compliance when searching for the robot.
- Sample and Reagent Conservation: if you work with precious materials and need to minimize sample and reagent consumption or work in the sub-microliter range, look for a system that offers minimum dead volume such as the Beckman Echo, iDOT, and MNATIS.
- Maintenance and Support: evaluate the maintenance requirements and the availability of technical support, service contracts, and spare parts. I highly recommend purchasing the service contract when acquiring a liquid-handling robot. It would cost 5-10% more, but it will pay off in the long term. The service contract covers maintenance, and engineering time to help with hardware and software issues.
- Cost and Budget: consider the initial purchase price, ongoing operational costs, and the overall cost of ownership within your budget constraints. Furthermore, consider the cost of training programs and user support to ensure that your team can operate the robot effectively. Entry-level liquid handling workstations (such as Opentrons OT-2) cost $5-$50k, and mid-range systems (such as Agilent Bravo, Tecan Evo, Hamilton STARlet) fall in $100,000 to $200,000, depending on the configuration. High-end liquid handling robots (such as Hamilton Vantage and Tecan Fluent) can cost $200,000 to $500,000 or more. Custom or integrated solutions can range from $200,000 to over $1 million or more, depending on the complexity of the automation and integration requirements. Alternatively, you can consider purchasing used or refurbished systems to save 30-50%. In this case, I highly recommend buying the system from a reputable vendor and performing the accuracy, precision, and robustness evaluation in-house.
- User Community and Reviews: explore user communities, especially internal ones in your company, forums, and reviews to gather insights and feedback from other users who have experience with the robot. In most cases, it will be more cost-effective if you acquire the same brand that currently exists in your company. This allows knowledge- and cost-sharing across the company.
Selecting the right liquid-handling robot involves careful consideration of your specific application requirements, workflow, and budget constraints. It’s essential to choose a system that can meet your immediate needs and accommodate potential future expansion or changes in your laboratory’s work. Most vendors offer no (or low)-cost demo contracts so that you can test the robot in-house before purchasing.
These were my thoughts but you can check these two papers for a more detailed review of the current automatic liquid handling technologies with a focus on bio-based labs. https://www.sciencedirect.com/science/article/pii/S247263032201679X
https://www.sciencedirect.com/science/article/pii/S1369703X22003825
In summary, introducing liquid-handling robots to your lab can be costly and time-consuming initially. However, in the long run, the investment will pay off by improving the accuracy/precision and reducing FTE time. Let us know in the comment section what your experience with liquid-handling robots is.
If there is a topic that you would like to see here or have a question, please drop us a line at hello@assay.dev
Happy Automating!